Primarily utilised by aircraft manufactures, EFGLAS equipment wire cables provide extreme strength, abrasion and temperature resistance by using a combination of PTFE tape and a PTFE impregnated glass yarn braid, over a nickel-plated copper conductor.
EFGLAS Equipment Wire FAQs
Key Characteristics
- Excellent resistance to fuels, hydraulic fuel, petroleum and ester based oils
- Operating temperature: -75°C to 260°C
- 600V Rating
- Nickel Plated Conductors
- Non-flammable
Typical Applictations
- Aerospace and Aircraft Wiring
- Industrial applications in extreme environments where high tensile strength is required
Product Data & Specifications
Cable Types Available
Screened, Screened and Sheathed, and 2 & 3 Core Versions Available
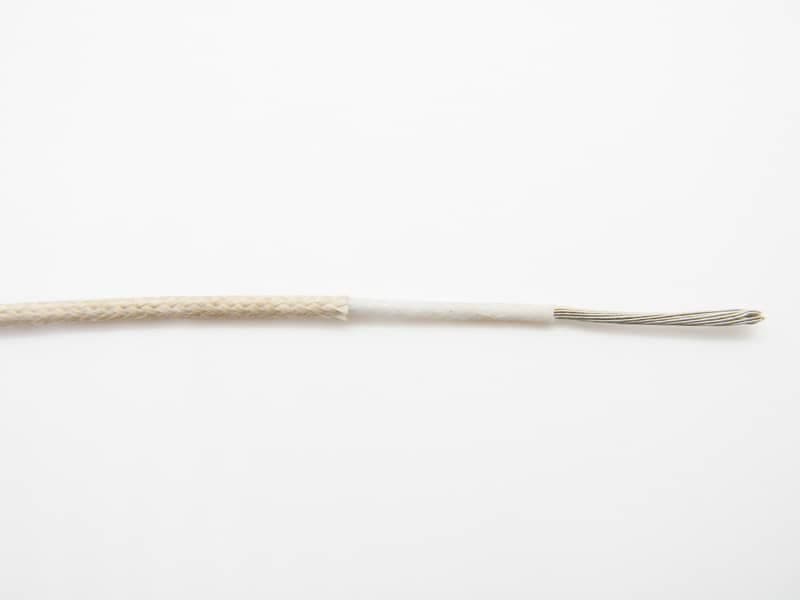
Can't find what you need?
Product Downloads
You may also be interested in
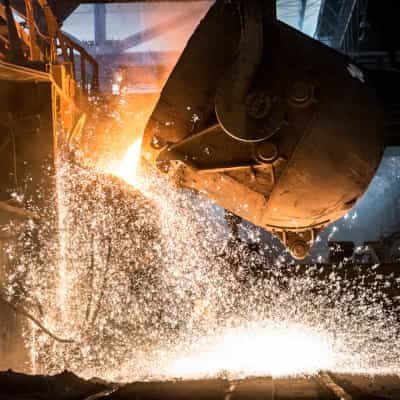
Heat Resistant Cables
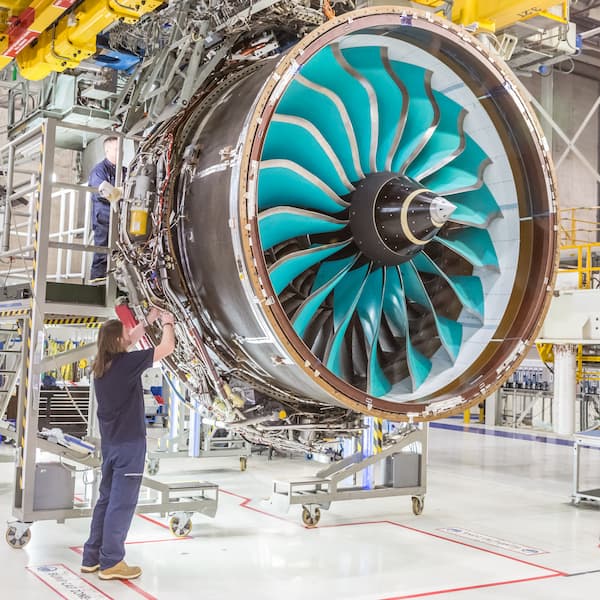
Aerospace Cables
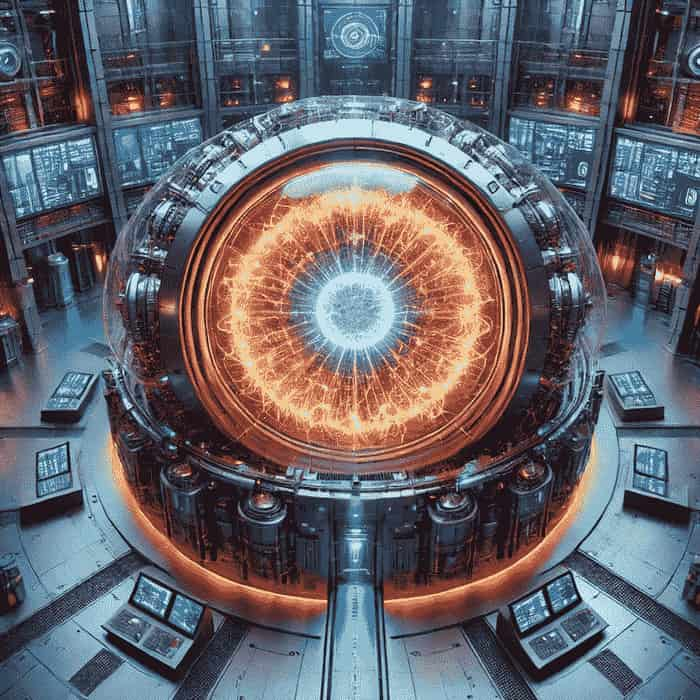
Radiation Resistant
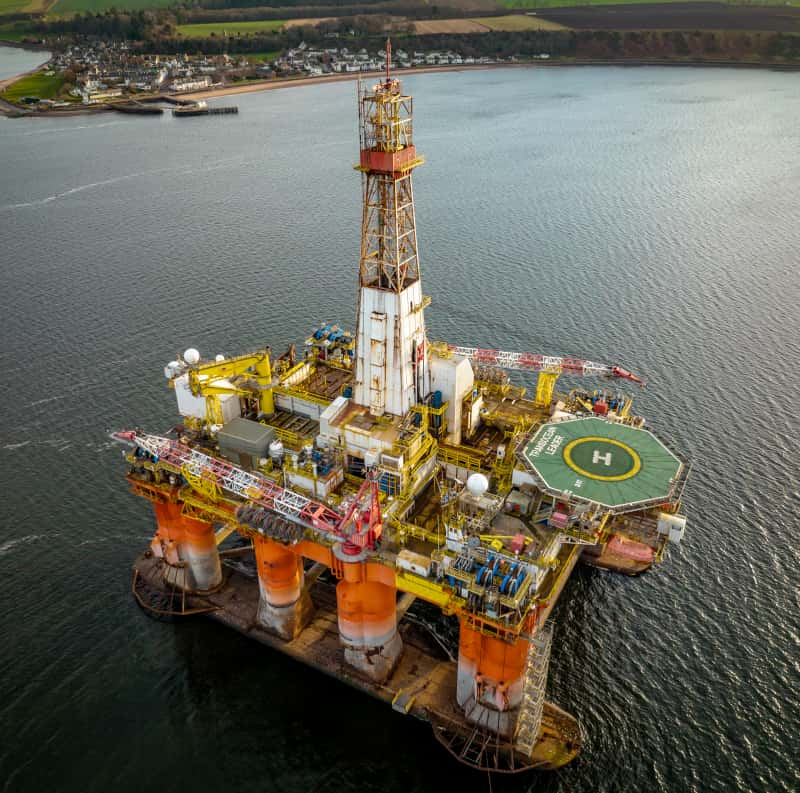
Oil & Gas Cables
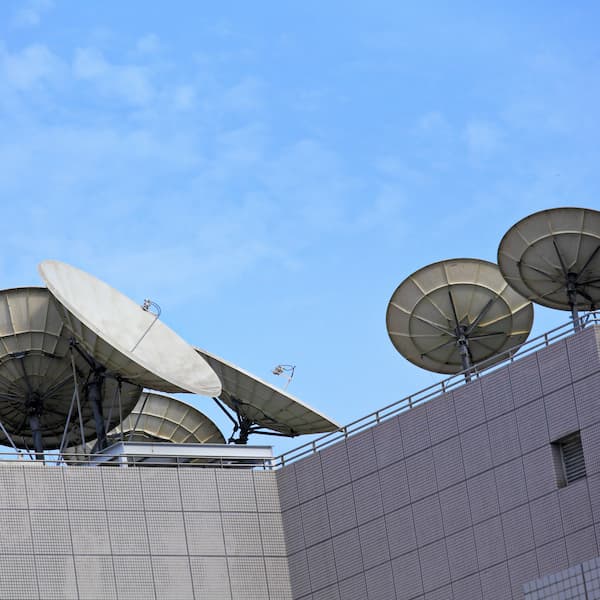
General Industry Cables
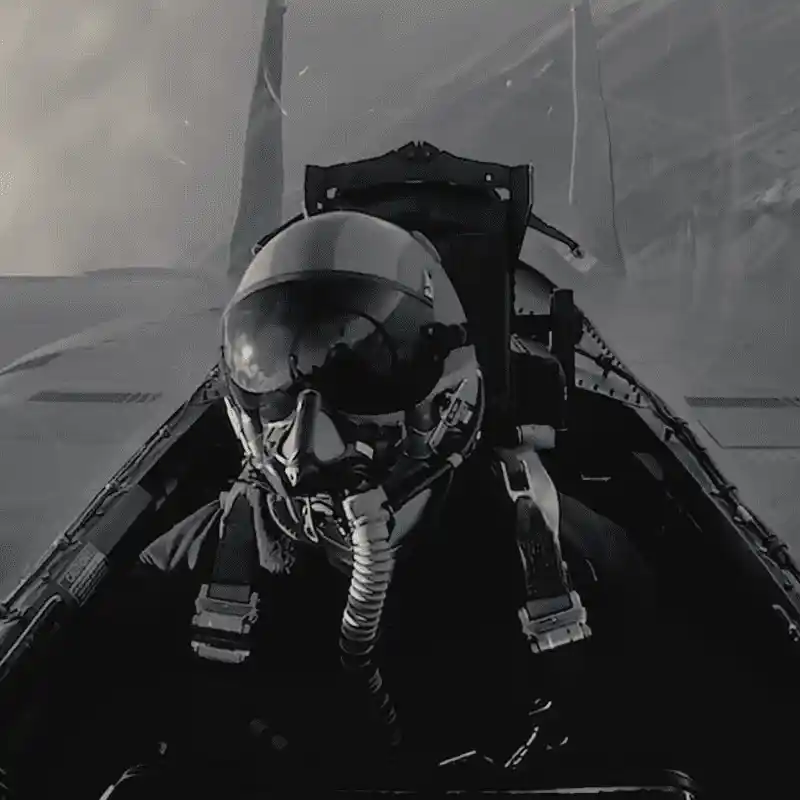
Research & Development Cables
Our Equipment Wire Range
EFGLAS Equipment Wire & Cable
View range
PFA Equipment Wire & Cable
View range
FEP Equipment Wire & Cable
View range
ETFE Equipment Wire & Cable
View range
PTFE Cable & Equipment Wire
View range
POLYIMIDE Equipment Wire & Cable
View range
PEEK Equipment Wire & Cable
Equipment Wire & Cables FAQs
What cable manufacturing processes are used to protect electrical and signal cables used in extreme heat and radioactive environments?
If you are looking to protect electrical and signal cables used in extreme heat and radioactive environments , you need plenty of layers which have specific protection capabilities. Heatsense apply the following cable manufacturing processes including braiding, extruding, and coating with heat and/or radiation-resistant materials as well as various liquid ingress protection coatings. The specific process used depends on the requirements of the application.
What materials are used for extruding coatings on cables for extreme heat and radioactive environments?
Materials commonly used for extruding coatings on cables for extreme heat and radioactive environments include polytetrafluoroethylene (PTFE), ethylene tetrafluoroethylene (ETFE), and fluorinated ethylene propylene (FEP). These materials have excellent temperature and chemical resistance properties.
In the manufacturing process, how are cables tested for resistance to extreme heat and radiation?
Cable manufacturers like Heatsense test for resistance to extreme heat and radiation using a variety of methods, including thermal cycling, radiation exposure (carried out by a specialist partner), and mechanical testing. Testing is typically done in accordance with industry standards to ensure accurate and reliable results.
What is the typical lifespan of cables manufactured for use in extreme heat and radioactive environments?
The lifespan of cables used in extreme heat and radioactive environments depends on a number of factors, including the materials used, the level of exposure to heat and radiation, and the application requirements. Cable manufacturers can provide guidance on the expected lifespan of cables for specific applications.
Can cables be customized to meet specific application requirements for extreme environments?
All Heatsense cables can be manufactured to order, therefore can be customized, combined into multi-strand configurations and braided into a single large cable to meet any specific application requirements for extreme environments. We are constantly innovating with our cables and can work with you to develop a customized solution that meets your unique needs.
How are cables manufactured to protect them against corrosion in extreme environments?
Heatsense cables are manufactured to be protected against corrosion in extreme environments by using materials that are resistant to corrosion, such as stainless steel and a range of plastics. Additionally, a range of different coatings can be applied to further protect the cables from corrosion. Heatsense cables design team will support you in choosing the right materials and coatings for your specific application.